
Silicon Carbide: The “Perfect Point” for Carbon Fiber Brake Pads
At present, brake pads are one of the most critical safety parts
Release time:
2018-08-13
Source:
At present, brake pads are one of the most critical safety parts in the braking systems of heavy machinery such as cars, trains, and aircraft and tanks. The quality of the material of the brake pads directly affects the braking performance of the vehicle and is more related to the safety of the driver's life.
The low density, good oxidation resistance, high temperature resistance, and corrosion resistance of silicon carbide make it occupy an important position in the field of brake systems. At the National Science and Technology Awards Conference held in January 2017, Academician Zhang Litong of Western Technology University won the second prize of National Technology Invention Award for "Silicon Carbide Ceramic Matrix Composite Aircraft Brake Disc Application Project." Status.
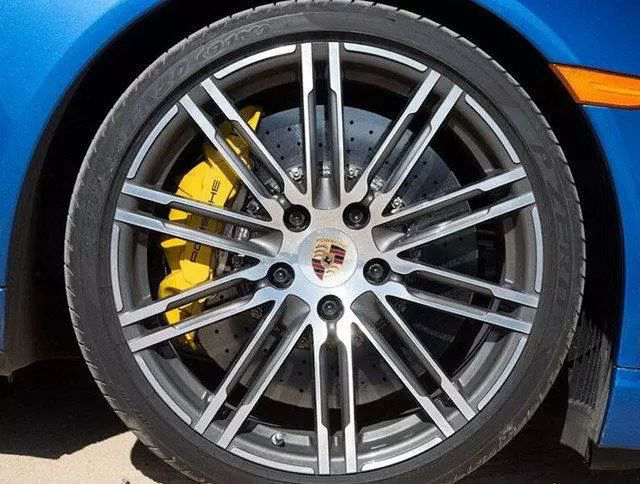
Figure 1 Porsche brake pads (Image source: Cheshenbang.com)
In order to further understand the application of silicon carbide in the field of brake pads, let's start with the performance of ideal brake pads.
◀ Ideal brake pads
In the car's braking system, the brake pads are the most critical safety part. The vehicle's deceleration and stop are all achieved by the friction between the brake pads and the brake disc. The ideal brake pad should have the following properties:
Table 1 Performance requirements and interpretation of ideal brake pads
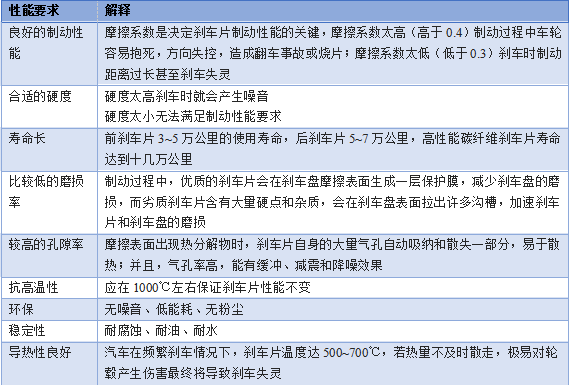
Icing on the cake
▶
Brake materials have undergone several generations of development from cast iron, steel materials, aluminum-based composite materials, C / C composite materials (hereinafter referred to as "carbon-carbon materials") to C / C-SiC composite materials (hereinafter referred to as "carbon ceramic materials"). Among them, powder metallurgy materials have defects such as high density, easy oxidation, and short service life. Carbon-carbon material brake pads have the advantages of smooth braking, low wear loss weight ratio, and large heat capacity on the basis of overcoming the defects of traditional materials.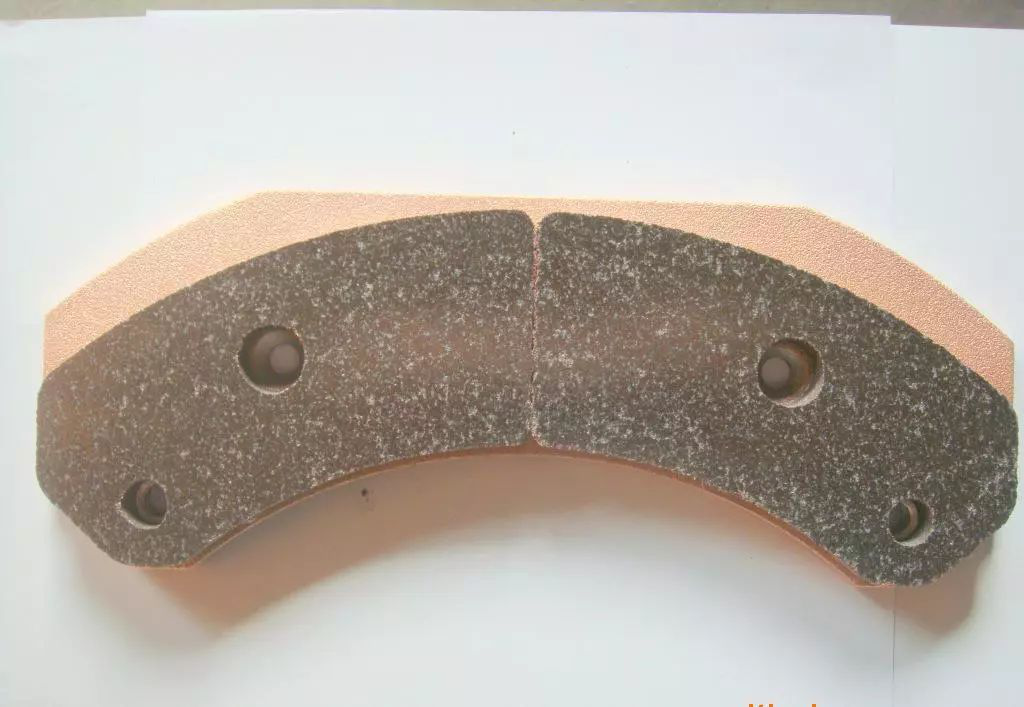
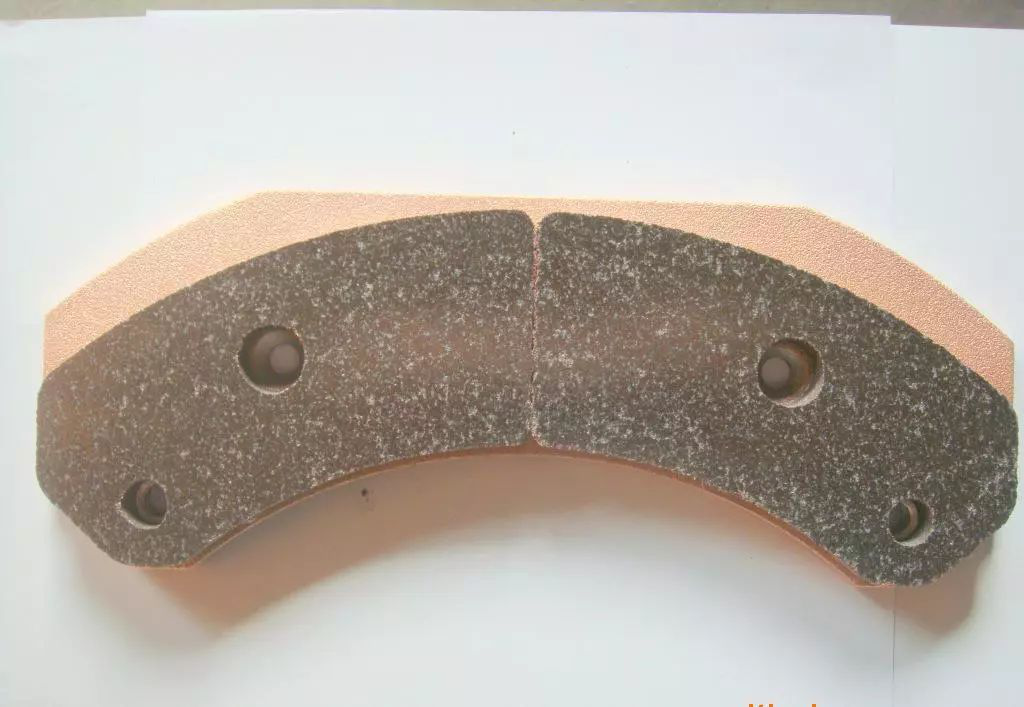
Figure 2 Copper-based powder metallurgy brake pads (Image source: HC Network)
Carbon materials are mainly composed of carbon fiber, graphite, and free carbon, while carbon ceramic materials are based on carbon carbon materials and are added with silicon carbide ceramics, so they are called carbon ceramics. The addition of silicon carbide has greatly improved the performance of carbon and carbon materials. Next, compare the specific tables to see how silicon carbide paints the "final touch" for carbon-carbon materials.
Compete among masters ▶
Carbon materials and carbon ceramic materials belong to the "nobility" of brake pads. They both have low density, large heat capacity, wear resistance, corrosion resistance and other outstanding advantages. The comprehensive performance is unmatched by ordinary semi-metal brake pads. A set of Brembo brake systems imported from Italy is tens of thousands of yuan. The master's tricks can be compared in terms of mechanical properties and friction properties.
Figure 3 The Brembo brake system is expensive (Image source: China Design Window)
Researchers have prepared carbon-carbon composite materials through chemical vapor infiltration (CVI) processes, with a density of 1.7-1.75 g / cm3 and a carbon fiber volume content of about 30%. Carbon-ceramic composite materials use CVI combined with reactive melt infiltration (RMI). Prepared by the process, the density is about 2.1g / cm3, and the volume content of carbon fiber is about 30%. The mechanical properties were measured through a series of mechanical experiments, and Table 2 was obtained.
Table 2 Comparison of mechanical properties between carbon and carbon materials
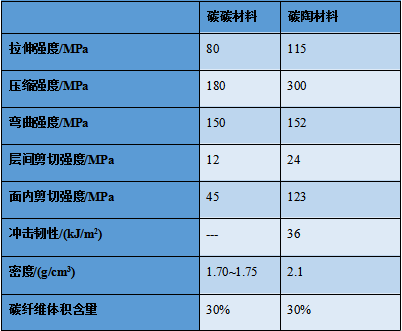
According to Table 2, it can be found that carbon-ceramic composite materials exhibit better static mechanical properties than carbon-carbon materials, such as tensile strength, compressive strength, interlaminar shear strength, and in-plane shear strength. %, 67%, 100%, 173%. Carbon ceramic materials also show excellent impact resistance, impact toughness up to 36kJ / m2, which is comparable to metal materials.
The researchers tested the friction properties of carbon-carbon and carbon-ceramic brake materials using an electric simulation inertia test bench, and obtained Table 3. Table 3 compares the dynamic friction coefficients of the two materials under different environments.
3Table 3 Comparison of friction properties between carbon and carbon materials
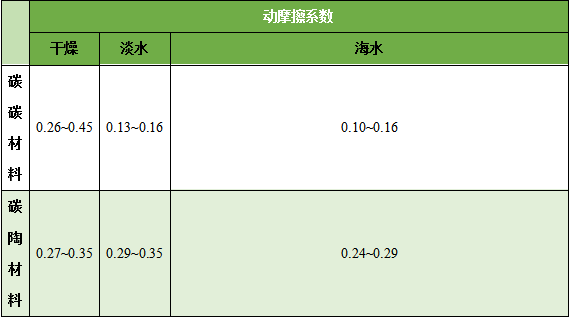
According to Table 3, it can be found that under the conditions of freshwater and seawater, the friction coefficient of carbon-carbon materials has decreased significantly, while the dynamic friction coefficient of carbon-ceramic materials has not changed due to the addition of silicon carbide.
In summary, the addition of silicon carbide makes the carbon-carbon material no longer afraid of water, salt and other environments, and its wet and dry friction coefficient is equivalent. At the same time, silicon carbide increases the density of the carbon-carbon material, enhances the overall mechanical properties, and even impact toughness. The metal materials are comparable.
◀ Summary ▶
C / C-SiC composites will undoubtedly be the new generation of brake pad materials. At present, carbon-ceramic brake pads have been used in Porsche 911, Pagani Zonda R and Lamborghini LP700. But the best is the best. High-performance products do not necessarily mean that they will have the best results. Whether they can exert their own advantages depends on their use environment.
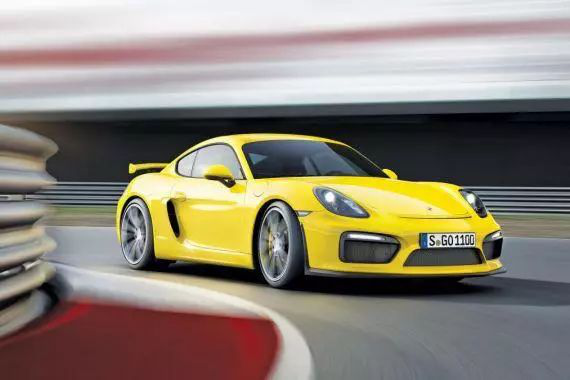
Figure 4 Carbon ceramic brake pads are still used on the Porsche GT4 (Image source: Sina Cars)
For the use of carbon and carbon materials and carbon ceramic materials for automobiles, some properties actually have "excessive performance". In general use environment, its relatively excellent performance such as oxidation resistance, heat transfer effect, wet and dry friction effect is not so important. For example, Ferrari's Formula 1 car uses carbon-carbon materials, but Ferrari's 458 uses carbon-ceramic materials. This is because the carbon-carbon material has a higher friction coefficient and enhanced braking capacity under heavy loads. This is undoubtedly favored by racers who seek extreme speed; on the contrary, the friction coefficient of carbon-ceramic materials is too stable and does not follow the load. Change changes, so it is more suitable for drivers who seek safety and comfort.
references
1. High-performance C / SiC brake materials and their optimized design; Tian Guanglai, Northwestern Polytechnical University, Key Laboratory of National Defense Science and Technology for Ultra-High Temperature Structural Composites, Xu Yongdong, Fan Shangwu, Zhang Litong, Cheng Laifei; Technology Co., Ltd., Tian Guanglai, Ke Shaochang, Liu Haiping.
2. Research progress of C / C-SiC brake materials; Key Laboratory of New Ceramic Fibers and Composites, School of Aerospace Science and Engineering, National University of Defense Technology, Sun Guoshuai, Liu Rongjun, Cao Yingbin, Zhang Changrui.
Article from: Circle of powder: Fire Vision
material,resistance
Previous Page
Next Page
Previous Page
Next Page